The Story of the Barge
The making of the Filtering Environmental Barge

An innovative solution popped up...
The idea of the Flexible Filtering Environmental Protection Barge originally popped up due to the lack of capacity for collecting oil in shallow waters and effective control of oil pollution in the shallow-water zone along the Danish coasts.
Once the oil hits the coast, significant amounts of sand and other material must be collected (up to 50 times the amount of oil) and subsequently destroyed; and if the oil hits a rocky shore, it must be cleaned manually, which is extremely costly, and often creates a new pollution scenario. In addition, oil causes severe damage to the coastal zone’s fauna and flora.
Thus, we set out to develop a vessel that
• Is capable of operating in shallow waters (down to 0.6 m).
• Is easy to operate and does not require special training and current maintenance.
• Is easy to store, transport and handle on land and at sea (and by air if necessary) with commonly available equipment.
• Is quick and easy to deploy whenever needed (anywhere in the world).
• Has low CAPEX and OPEX (cheap in procurement, operation and maintenance).
We soon realized that to operate in shallow waters, a constantly shallow draft is required, which is best achieved by making the vessel’s collection/storage capacity and the surrounding water “connected vessels”. Thus the vessel had to feature holes in the bottom. To prevent collected oil-contaminated water from running back into the surrounding water, the vessel had to be equipped with a filter that stops the oil.
We performed a series of “kitchen table experiments”, which showed that the solution with holes in the bottom and a filter actually works.
It is important that the barge impact the environment as little as possible in both operation and maintenance, and if/when it may be obsolete and be disposed of in many years down the road. The environmental barge is therefore built in aluminum, which is 100% recyclable.
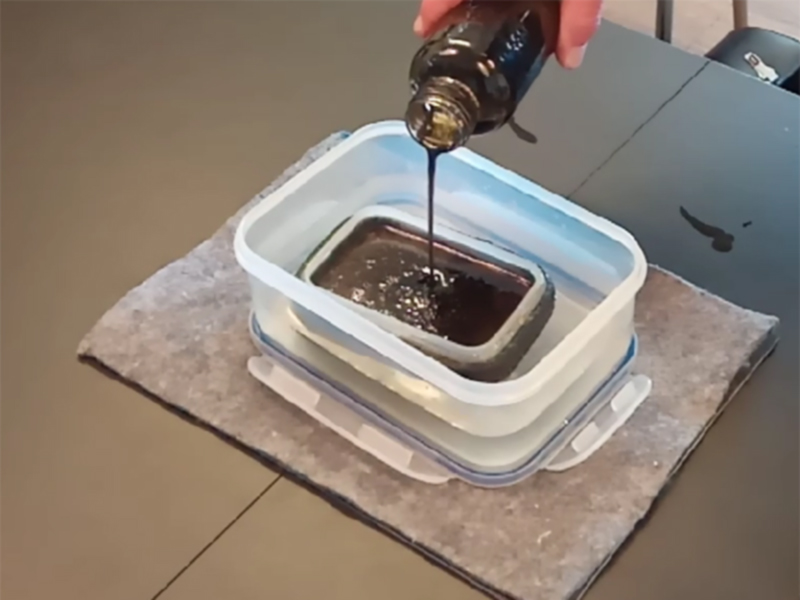

Building the FEB-I
Construction of the first FEB-I began at Søby Shipyard in Denmark in February 2022. The welding of the barge, which was essentially a large 3D puzzle in aluminum, was completed in 3 weeks by the shipyard’s skilled welders.
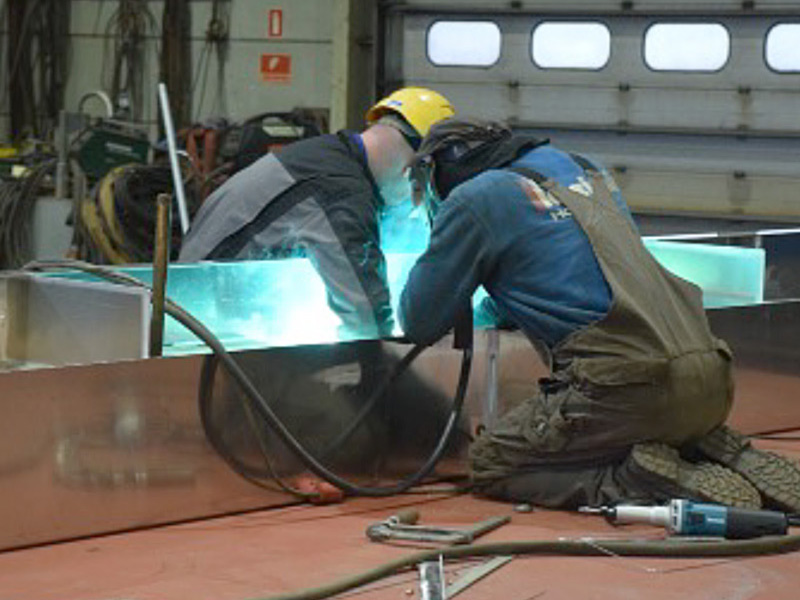
Obtaining patent for the FEB-I
In DEC 2021 FLEX-FEB filed an application with the Danish Patent and Trademark Office for a patent on the FEB-I and its unique features and capabilities.
After technical processing of our patent application, the Danish Patent and Trademark Office announced on 07 SEP 2022 that FLEX-FEB’s application had been approved and that a patent had been issued for the invention.
More international patents are now pending.
The fact that the flexible environmental protection barge is now patent-protected underlines FLEX-FEB’s ability to rethink oil spill response and coastal protection and provide an innovative and unique solution to the challenge.

Harbor Acceptance Test (HAT)
Shortly after completion of FEB-I at Søby Shipyard, the barge was launched and tested in one of the shipyard’s dry docks.
The barge’s stability and load-bearing capacity proved to be even better than expected, and all functional equipment (bulkheads, deck plates, mounting rods, skimmers, etc.) worked fine.
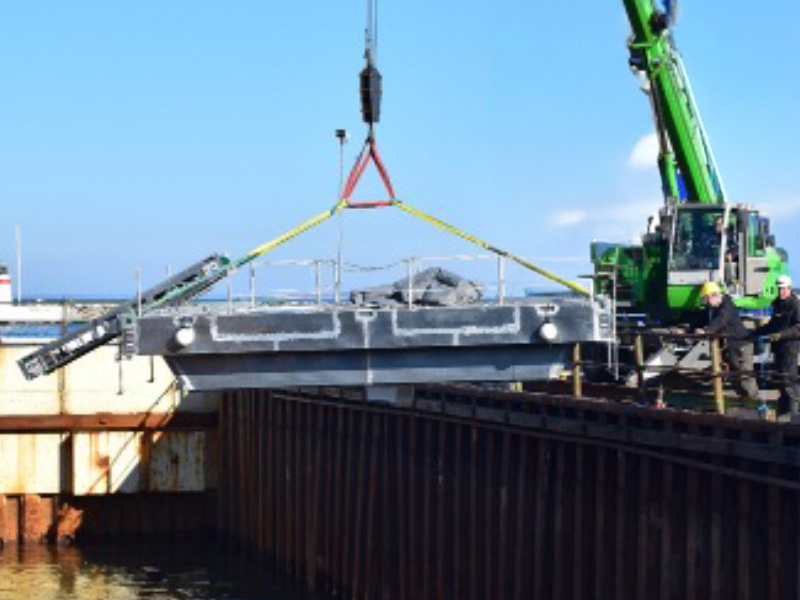
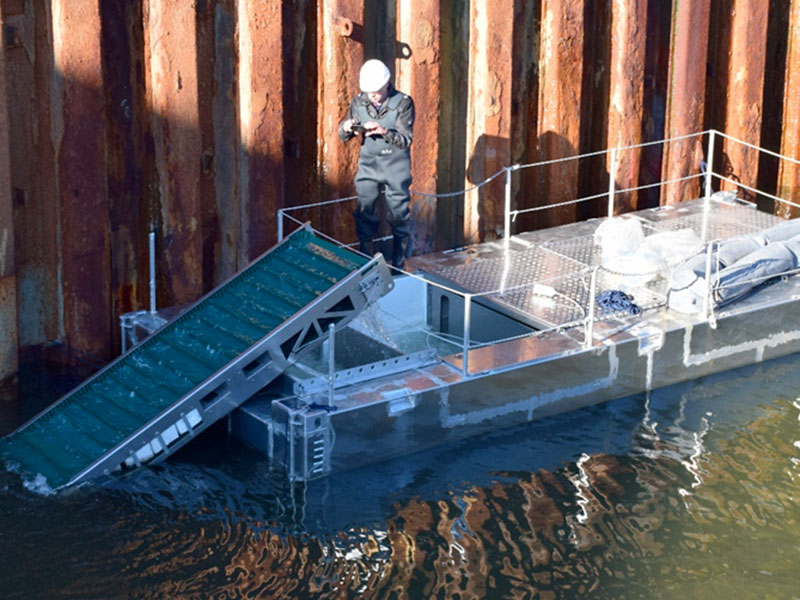

Sea Acceptance Test (SAT)
In JUN 2022 FLEX-FEB carried out two series of comprehensive Sea Acceptance Tests in the shallow waters off the coast of the island Aeroe in Southern Denmark in close collaboration with Aroe Sea Rescue Association (“Ærø Sørednings-forening”).
During the sea trials, FEB-I was towed at varying speeds in fresh winds (6 – 10 m/s) and light sea (0.5 m wave height) with and without oil containment booms on tow. FEB-I managed the sea well at speeds up to 3 knots.
In the operating area, FEB-I was connected to the oil booms, and popcorn (instead of oil) was thrown into the sea. The oil booms contained the popcorn and led them towards FEB-I where the remote-controlled belt skimmer collected the popcorn from the sea surface. The skimmer was remotely operated from the towing vessel, and thus it was not necessary to have personnel on board the barge during the operation.
The tests were performed with three different types of oil booms from two of the world’s leading suppliers of maritime pollution control equipment, and despite the different properties of the oil booms, they all worked well with FEB-I, thanks to the special mounting rods that allow the barge and the oil booms to move independently in the sea.
The SAT program demonstrated that
- Response time for the FEB-I is very short.
- Handling FEB-I does not require any special training. The barge can be quickly rigged and operated by a crew with common seaman background.
- FEB-I can be connected to several different types of oil booms, and can thus be used together with already available equipment.
- FEB-I is capable of, in one single operation, collecting oil-mixed water, filtering oil from water, directing the purified water back into the sea and store the oil, until it can be pumped into a tank farm for later recycling.
The SAT program demonstrated that
- Response time for the FEB-I is very short.
- Handling FEB-I does not require any special training. The barge can be quickly rigged and operated by a crew with common seaman background.
- FEB-I can be connected to several different types of oil booms, and can thus be used together with already available equipment.
- FEB-I is capable of, in one single operation, collecting oil-mixed water, filtering oil from water, directing the purified water back into the sea and store the oil, until it can be pumped into a tank farm for later recycling.